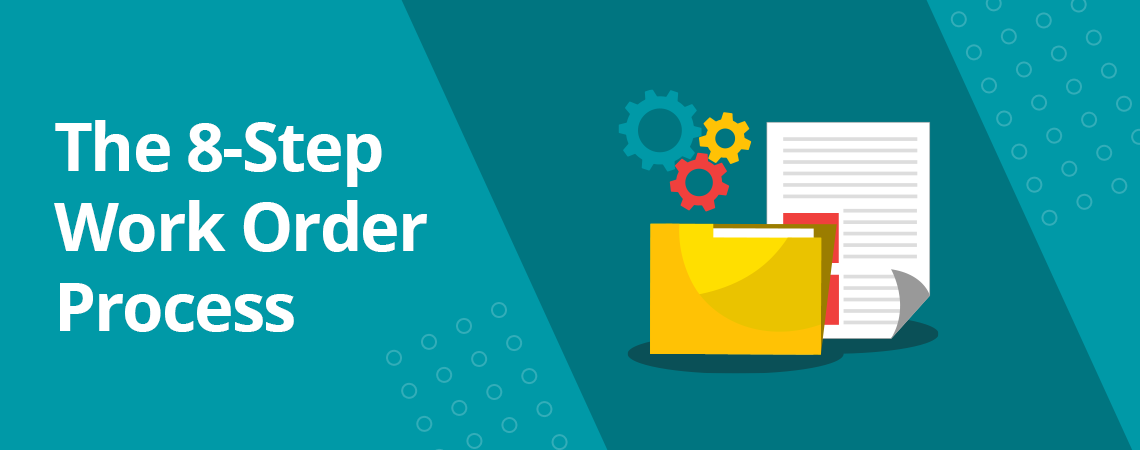
Guide to Creating the Perfect Work Order (Infographic)
Managing work orders effectively can be crucial to long-term business success. In doing so, you can empower your field service team to improve their job completion and first-time fix rates. So, what’s the secret? We’ve put together the ultimate guide to mastering work orders in 2021.
Contents
What is a work order?
A work order is a task or job that can be scheduled and assigned to a member of your team. It is a term typically used in the service and maintenance industry, where jobs are deployed to an engineer in the field. Usually, they are created in response to a new customer request, but they can also be created for follow-up inspections and audits.
Work orders can represent several different tasks including equipment repairs, installations or ongoing maintenance. Each one should be well-documented and shared with the field engineer it’s been assigned to. It should include detailed information about the task in hand as well as a proposed outcome and method for completion. Work orders can be either hand-written or created using digital forms and templates.
CMMS software, like Joblogic, helps field service businesses to plan and execute work orders more efficiently. From receiving a customer request, new jobs can be logged, scheduled and assigned to engineers digitally and in record time.
- Assign, prioritise, track and complete work orders in real-time.
- Document jobs and tasks using intuitive digital forms and templates.
- Capture and share new information with field engineers to help them complete jobs more efficiently.
What is the 8-step work order process?
To complete a work order, you need to follow a number of key steps. The following example from a reactive (unplanned) maintenance request will help to give you an understanding of how to create a simple work order software process using Joblogic software.
- Customer request: A team supervisor receives a request from a customer for assistance with a faulty HVAC unit on their premises. At this stage, it’s crucial for the supervisor to identify whether the job is a planned or unplanned maintenance task. This will determine the level of urgency associated with a new job.
- Create a new work order: The supervisor logs the request in the system and creates a new order. He also logs the customer details, site address, job instructions, compliance forms and other relevant information that will add context.
- Assign the work order: Before assigning the order to a field engineer, he checks his team’s availability using the system’s real-time scheduling calendar. Once done, he deploys the job directly into the diary of the most suitable engineer. Using a tool, like Joblogic, makes it easy to identify an appropriate date and time to assign new jobs. The engineer will be kept in the loop at all times thanks to the real-time sync between the back-office and his smartphone.
- Work order received: The engineer receives the new order on his/her mobile device along with all relevant job information. It is a simple tap of a button to notify the supervisor that he has accepted the new job.
- Appointment reminder: On the day of the job, the supervisor sends an automated appointment reminder to the customer via SMS or email, letting them know that their engineer will be arriving on-site at their pre-scheduled time. He can also optimise the travel route of his engineer using the software’s intelligent route planning feature.
- Complete the work: Upon site arrival, the engineer will be prompted to fill out any mandatory compliance forms and checklists using the Joblogic mobile app. He can also capture new information on the go including site notes, timesheets, customer signatures and GPS-stamped photos.
- Invoicing: Once the order is complete, the engineer can automatically send a job report to the office and customer alike. In minutes, an invoice can be raised and sent to the client electronically (either via email or the customer portal.)
- Happy customer: The end result is a job well done and a customer who is wholly satisfied with the service.
With Joblogic, the work order process will be quick, simple and efficient. By syncing our software with your engineers’ smartphones, they’ll be ready to respond to a new work request immediately.
- Build, store and share work order templates in real-time.
- Leapfrog competitors by streamlining work order management and completing more jobs per day.
What should a work order template include?
A work order template (or document) should include every detail about a maintenance task. It should outline the process for completing a task, who authorised it, who it’s assigned to and the agreed outcome. In essence, a work order template should provide a complete guide for a field engineer to follow.
- Dates and times: This should include the date at which the work order was created as well as the expected and actual completion dates.
- Original point of contact: Reference of who created the order.
- Asset: A detailed specification of the equipment that needs fixing.
- Description of issue: A detailed specification of the customer’s problem.
- Scope of work: A breakdown of what work is required to complete the job.
- Parts and tools required: Notes of any parts that may need replacing.
- Health and safety notes: A full checklist of industry-standard safety procedures.
- Task checklist: The steps required to complete the work order.
- Priority: A note specifying the urgency of the task in hand.
- Assigned to: This specifies who will be doing the work whether it be a company engineer or a contractor.
- Associated documents: Relevant resources that can help the engineer complete the order efficiently. This could include SFG20 checklists, manuals and diagrams, videos, asset and service histories, purchase orders, and images.
- Notes: Additional information that could assist the engineer in completing the work order. This could detail troubleshooting techniques made previously on-site.
Final Thoughts
Work orders are key to an effective maintenance operation. When properly managed, they give your business stability and structure to become more efficient. 2021 is the year to choose the right tools to do just that. Book a free demo of Joblogic today and see your preventive and unplanned maintenance completion rates soar.