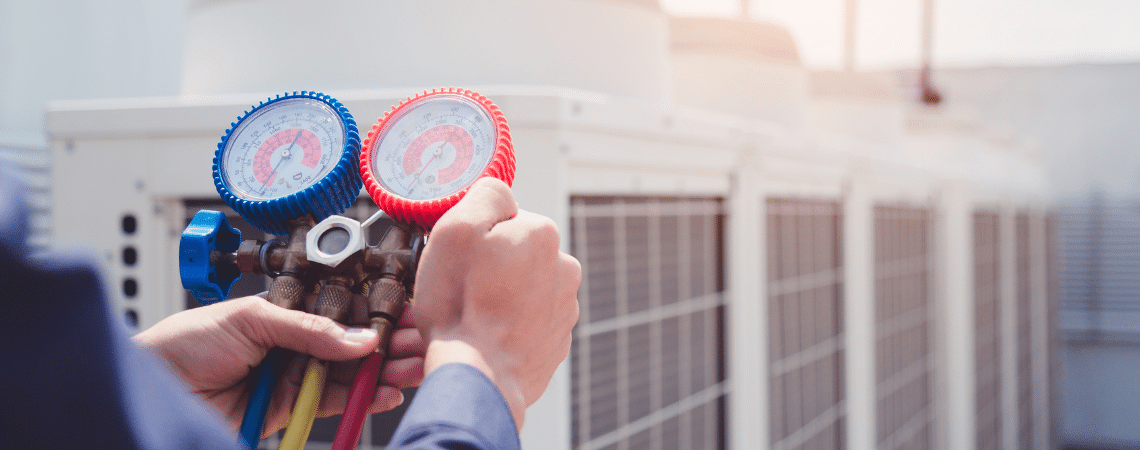
Maximising productivity of your HVAC engineers through workflow automation
The HVAC service software sector is a competitive place to be. Your customers have no shortage of options for where they can get their HVAC units serviced, which means as a business you’re constantly fighting to maintain the standard of service that customers expect. Meaning that issues such as recruiting HVAC engineers can have a dramatic effect on your business if you’re not able to work around them. Thankfully, you can offset this by maximising the productivity of your existing engineers.
How do you do this? One of the most effective ways is by using workflow automations which provides a range of benefits that ultimately result in improving HVAC engineer productivity.
The benefits of workflow automation for HVAC engineer productivity
Time savings
With workflow automation the time spent on administrative tasks is reduced significantly. Rather than spending time manually creating invoices or purchase orders, your engineers can quickly select the correct information and have what they need to be generated on their device instantaneously, allowing them to complete jobs sooner, travel to their next job, and communicate with your back-office staff in real-time.
Enhanced efficiency
Even the best HVAC engineers make mistakes and it’s well-known that manual errors can cause delays in the operational process. With work automation, you can eliminate manual errors by standardising processes for engineers, as well as standardising data that’s collected about the job. With standardised processes and data collection, engineers will know exactly what sort of information is available to them, they can access this before they begin the job to plan accordingly, resulting in increased efficiency, productivity, diagnostics and resolving HVAC system issues.
Improved collaboration
As workflow automation standardises data collection, you will see further benefits across your business. Rarely will the same engineer be responsible for follow up jobs, which means that being able to pass over relevant information is important. With workflow automation, information can be shared in real-time, as well as having accurate historic logs of completed work, which parts have been replaced, and what issues have been resolved. Access to this sort of data and information leads to more coordination and better communication across engineers and teams.
Enhanced customer experience
Perhaps most importantly, with workflow automation, you can streamline service request response times and issue resolutions, which keeps your customers happy, and encourages them to continue to come back to you for their HVAC support needs year after year.
How to deploy workflow automation to improve HVAC engineer productivity
Improving HVAC engineer productivity is something that can be achieved through multiple forms of workflow automation. Automating one area isn’t enough, to maximise productivity, you need to automate as many of your business processes as possible. Based on our experiences working with HVAC service software companies, we’ve found the following areas to be the most effective when it comes to deploying workflow automation to improve HVAC engineer productivity.
1. Service request management
Sometimes boosting your HVAC engineer productivity isn’t about how they spend their time, but how you assign their work. If your office team spends ages working out whose best suited to the job, workflow automation allows them to assign HVAC service jobs quickly and efficiently, and your engineers will be told about the new job as soon as it’s been assigned to them. Even your customers can benefit from automation! If they submit a job request through a customer portal it will automatically be logged and tracked, allowing for quicker response times.
2. Planned preventive maintenance scheduling
Don’t rely on your office team to remind engineers about scheduled PPM jobs. With the right workflow automation in place, jobs can be set months in advance, and will appear in the engineer’s job list when the scheduled time arrives. They can set up recurring maintenance schedules for individual assets, or groups of assets, and the system will automatically create work orders for your engineers that will have all the relevant information that they need for the job. This includes task details, checklists, instructions and documentation, all of which they will need when they’re out completing PPM jobs.
Set up recurring maintenance schedules for individual assets or groups of assets and the system will automatically generate work orders or tasks for the scheduled maintenance. When automatically deployed to the field operative, these work orders contain all relevant information, including the asset details, required tasks, instructions, and any associated documentation.
Assign specific engineers or technicians, track their progress, and record completion status. Field operatives can access task details, including checklists, instructions, and documentation, through the Joblogic mobile app and if further clarification is required can liaise directly with back office staff using the direct messaging feature.
3. Inventory management
Running out of stock for parts that your engineers need is a sure-fire way to tank their productivity. Make sure that never happens by setting up alerts for when stock gets below pre-set levels. When these alerts go off, your team can raise new purchase orders to make sure that you always have enough parts in stock for your HVAC engineers to use.
4. Reporting & analytics
With automated data collection you can reap the benefits of better reporting and analytics. This will allow you to more easily track the KPI’s your engineers work towards, so you can identify potential areas of concern. You might want to review specific engineers who are missing their KPIs, or system-wide issues that need a broader approach to fix. By highlighting areas of concern among the KPIs you can then set about to improve your performance and boost your HVAC engineer productivity as a result.
5. Asset management
With a cloud-based field service management system in place, you can cut down on the amount of time that your HVAC engineers must spend duplicating work notes and associated asset information. All asset details will automatically upload across the system for back-office staff and other engineers to see. Accessing this data is easily automated as well. With the use of QR codes all your HVAC engineers need to do is scan the QR Code and they’ll be taken to the relevant asset registry, allowing them to see all the information they need to know, and to add their own updates as needed!
These are just a handful of the ways that you can deploy workflow automation to boost HVAC engineer productivity. If you’d like to learn more about how to improve business process through workflow automation, or how HVAC software can help you grow your business, then book a demo with our team of experts who will happily answer any questions you might have.