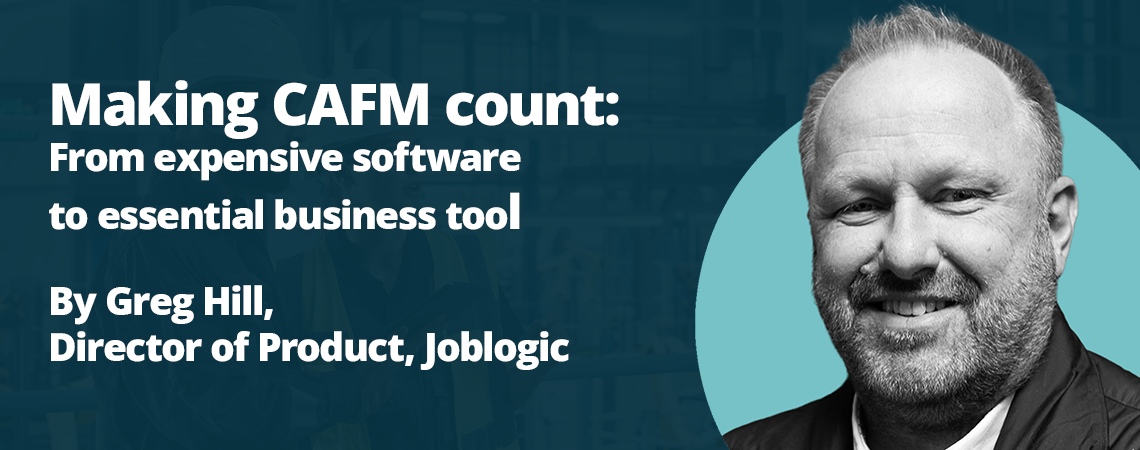
Making CAFM count: From expensive software to essential business tool
After 30 years in facilities management, I still see facility managers struggle to extract the full value from their CAFM systems.
The red flags are obvious once you look for them.
Contractors and their engineers still use paper forms on site, job updates come via phone call instead of the system, asset lists are incomplete or full of duplicates, and accurate reports are impossible to generate.
But most of all, I see a growing gap between those with ineffective CAFMs and excellent ones. The thing is, this gap isn’t really about the technology, it’s about how the system fits specific workflows, whether your team sees its value, and–crucially–whether it makes their jobs easier.
When you get it right, your CAFM transforms from software expense to the backbone of your entire operation. It becomes the central nervous system that connects every aspect of your facilities management, from the engineer on site to the boardroom budget meeting.
The good news is that improving your system isn’t too complicated. These four proven steps have helped countless facilities managers unlock the full functionality of their CAFM systems.
Step 1: Drive widespread adoption through ease of use
The fastest way to improve the performance of your CAFM is to ensure people use it. Sounds obvious, but I’ve seen too many implementations fail because they focused solely on features.
The key to adoption is making the system work for users, not just the manager. That means clean interfaces, time‑saving functionality, and simple job flows.
For contractors and engineers, the fix isn’t more training or stricter policies. It’s a system experience that makes reporting fast and simple with offline capability or photo annotation.
For asset managers it’s removing duplication with other systems, like finance or HR, so information is accurate and easy to access, and doesn’t need updating in multiple tools. Driving adoption is one thing, but to keep people using the system, you need to make them feel like their contribution matters.
When engineers see fewer repeat callouts because their photos and notes were clear, or site staff see how logging a fault leads to a fast response, they buy in and keep using the system.
I’ve found the best way to drive initial adoption is to pick your champions wisely. Find the engineers who are already tech‑savvy, get them on board first, and let them influence the rest.
When the team sceptic sees their colleague closing jobs faster and getting home on time, they start paying attention.
Widespread CAFM adoption is the single biggest efficiency improvement you can make. And once you get it right, it unlocks a whole lot more opportunities for efficiency from your system.
Step 2: Become compliant by default
The next big efficiency play is configuring your CAFM system to streamline your compliance.
Compliance isn’t about ticking boxes–it’s about proving you’ve kept people safe. With widespread adoption, your CAFM is now collecting digital signatures, photos, and timestamps to prove work is done correctly.
But the magic happens when everything connects.
By linking specific job types with mandatory checks and documentation you can create an audit trail of who did what, when, and where. That way, when certificates are missing, expired, or pending review, your CAFM system automatically alerts managers.
And it’s an even bigger time saver when the auditors inevitably come knocking. You’re not searching through shared drives or chasing subcontractors for records.
Everything you need is right there in the system. Need to prove you’ve maintained something properly for the past five years? It’s all there, searchable and timestamped.
Step 3: Make decisions based on real‑time data
With adoption and compliance covered, you have a sea of clean, current data that can shift you from firefighting to forward planning. This is where your CAFM stops being a record‑keeping system and becomes a strategic tool.
Real‑time dashboards track which contractors are performing, where your most problematic assets are, and where you’re spending the most time and money. But raw data isn’t insight–you need to ask the right questions!
For instance, when you can see Machine A has 40% more callouts than Machine B, you can investigate why. Maybe it’s older equipment, maybe it’s poor maintenance practices, or maybe it’s just increased usage.
Without data, you’re guessing. With it, you have answers.
Real‑time data means catching problems before they escalate.
A job running late? You know about it before the client calls.
Costs trending high at a particular site? You can investigate before month‑end.
It’s the difference between being reactive and being in control.
But live data doesn’t just help you solve problems, smart FMs use real‑time data to negotiate better contracts with suppliers, identify training gaps in their teams, and justify future capital investment.
Step 4: Unlock predictive maintenance
You’ve mastered adoption, streamlined compliance, and unlocked the data. What’s next?
Advanced facility managers are linking the operational data captured in their CAFM with machine sensor data, like vibration, temperature, and pressure, to deploy predictive maintenance models to anticipate failures and avoid them.
By tracking how long jobs take, which assets fail repeatedly, and what parts are used where, patterns emerge. That problematic air handling unit that breaks every three months? Your CAFM can flag it for replacement before it fails again, not just schedule another repair.
And the difference between managing failures and preventing them is huge: reduced downtime, fewer emergency callouts, extended asset life, and more.
The beauty of predictive maintenance is that you can start small. Pick one critical asset type – perhaps your pumps or air handling units. Track every intervention for three months: failure types, parts used, time taken, environmental conditions. You’ll quickly spot patterns that help predict future failures.
This isn’t theoretical, it’s already happening in advanced environments, and when your CAFM systems are in order, you can begin planning ahead with confidence, too.
Make the most of what you’ve got
Technology alone won’t transform your FM operation. But the right tools, used in the right way, can absolutely help you do more with less.
I’ve learned that successful CAFM deployment isn’t about picking the perfect system, it’s about being honest about how your team works and choosing technology that supports them.
By taking practical steps to optimise how your CAFM system is adopted, configured, used, and maintained, you can build a more efficient, proactive, and data‑driven approach to facilities management – one that works for you and your people on the ground.