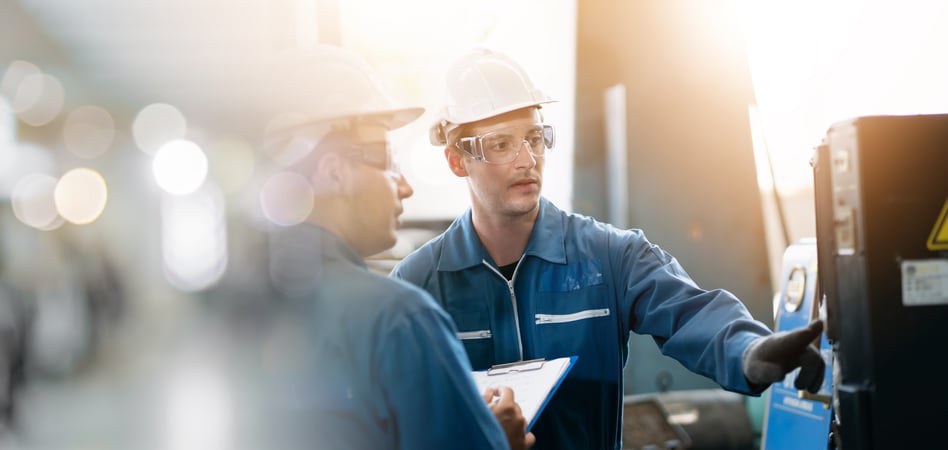
Maximising Efficiency: Maintenance Management Best Practices
Maintenance Management Best Practice 1: Focus on Preventative Maintenance
Most organisations are still operating on a reactive maintenance model. This means that maintenance occurs when an asset breaks down. Whilst it’s better than leaving an asset not functioning, maintenance management strategies that focus on reactive maintenance have been shown to increase costs and equipment downtime and negatively impact the efficiency of businesses. Instead, what you should be focused on is Preventative Maintenance Management (PPM)
What is Preventive maintenance?
Preventive maintenance management (PPM) is the cornerstone of maintenance management best practices. With a PPM approach, you don’t just sit there and wait for equipment to break down. Instead, you take proactive steps to prevent equipment downtime before it occurs. This is done through regular inspections of assets and equipment, servicing assets, and replacing parts.
The idea is that by addressing issues pre-emptively, you can avoid costly repairs, lower your costs, increase the reliability of your equipment, extend asset lifespans and make regulatory compliance more manageable.
Effective PPM best practices require you to schedule regular maintenance visits for your assets. While this can be done in a way similar to your current operation, it is also possible to use the wisdom of the crowds and utilise the best practices that have been established over time by following best practice maintenance management schedules like SFG20.
Maintenance Management Best Practice 2: Streamline your workflows for more efficient daily operations
Daily operations for most businesses could be more efficient. This isn’t a surprise, as much time gets wasted covering basic repetitive actions that get performed daily. Without trying to streamline your daily operations, more time is spent handling administrative tasks, and less time is spent on actions that provide real value to the business. This leads to increasing waiting times for maintenance tasks, leading to an increased likelihood of equipment breakdowns, shortened asset lifespans and, ultimately, higher operating expenses. Following maintenance management best practices and streamlining your daily operations will free up time to spend on more valuable activities.
How do you streamline your daily operations for maintenance management?
To streamline your daily maintenance operations, you must understand what tasks you complete daily. Often, for maintenance, three essential processes are not streamlined:
1) Scheduling jobs for completion
2) Accessing relevant information to complete a job quickly
3) Compliance with regulations
Maintenance management best practices for job scheduling involve automating processes and making it easy to see and understand who is available to complete a job. With CMMS software or job scheduling software, you’ll have access to a complete list of your maintenance team members, see who is scheduled for jobs already, and see who has the skillsets needed to undertake a job that needs completing.
Once you’ve assigned a job, the software can even automate the process of letting the team members know they have a new job assigned to them through associated mobile apps. You’ll even be able to view the status of jobs in real time, giving you complete knowledge of what’s happening in the field.
To streamline the access to information, you need to give your team members access to information when they are in the field completing a job. Through CMMS systems and asset management software, you can provide your team complete access to every detail of the job and the asset history of the equipment being worked on. This means less time is spent catching up on what work has been completed before, and they can focus on getting the job done quickly. This results in jobs getting completed quicker, reduced asset downtime and lower operational costs.
Combining asset management and CMMS software also allows you to streamline compliance with regulations. By providing you with easy ways to ensure work is compliant, such as forms and checklists that the engineers must fill in before the jobs can be marked as complete, you’ll be able to make sure that work is done to the correct standard and have a place to store certificates you need to keep track of, all in one software.
Maintenance Management Best Practice 3: Focus on Your Performance Metrics
Without measuring performance, you don’t know what’s working and what’s not, which means you won’t be able to make data-driven decisions. However, you need to ensure you’re watching the right metrics. We recommend the following metrics be the core of your maintenance management strategy:
- Overall Equipment Effectiveness (OEE): OEE is a comprehensive metric that evaluates equipment performance, availability, and quality. It provides insights into how well equipment is utilised and identifies areas for improvement.
- Mean Time Between Failures (MTBF): MTBF measures the average time elapsed between equipment failures. A higher MTBF indicates greater reliability and longer intervals between breakdowns.
- Mean Time to Repair (MTTR): MTTR measures the average time to repair equipment after a failure occurs. Minimising MTTR helps reduce downtime and improve operational efficiency.
- Planned Maintenance Percentage (PMP): PMP compares the percentage of scheduled maintenance activities to total maintenance performed. A higher PMP indicates a proactive approach to maintenance, which can reduce unplanned downtime and extend equipment lifespan.
- Maintenance Cost as a Percentage of Revenue: This metric calculates the proportion of revenue spent on maintenance activities. It helps assess the cost-effectiveness of maintenance efforts and identify opportunities for cost reduction.
- Scheduled Maintenance Compliance: This metric measures the percentage of scheduled maintenance tasks completed on time. It evaluates the effectiveness of maintenance planning and adherence to maintenance schedules.
- Asset Utilisation: Asset utilisation measures the percentage of time that equipment is actively used for production or operations. Maximising asset utilisation improves productivity and efficiency.
- Inventory Turnover: Inventory turnover calculates how quickly inventory is used and replenished for maintenance, spare parts, and other purposes. It helps optimise inventory levels and reduce carrying costs.
- Work Order Backlog: The backlog quantifies the number of pending maintenance tasks or work orders. Managing and reducing the backlog ensures timely maintenance completion and minimises disruptions.
- Mean Time to Failure (MTTF): MTTF measures the average time until a failure occurs for a specific component or system. It helps assess the reliability and performance of individual parts or assets.
- Energy Consumption: Monitoring energy consumption associated with equipment can highlight inefficiencies or opportunities for energy-saving initiatives, contributing to sustainability goals.
- Safety Metrics: Metrics such as the number of safety incidents or near misses related to maintenance activities help evaluate the effectiveness of safety protocols and identify areas for improvement.
Maintenance Management Best Practice 4: Keep Your Team Training Up to Date
One of the most common ways that maintenance management can go awry is by not having the most up–to–date knowledge of assets and techniques for maintaining them. Similarly, if you’re using software like PPM, CMMS, CAFM, or Facilities management software, your team will need to fully understand the latest features and modules that are available.
By working with your software providers to ensure that your team is up-to-date with changes to the system through ongoing training programs, you can maximise the gains for your systems and get more benefits. For more generalised training, it’s essential to ensure that your team keeps up to date with training that’s legally required for you to be compliant and that they are updated on industry best practices, safety protocols and more. The best way to do this is to encourage a learning culture within your organisation and allow people to take responsibility for their personal development.
Maintenance Management Best Practice 5: Master Your Inventory Management
One of the most significant barriers to completing maintenance work is running out of parts. Running out of parts slows down the maintenance process and lowers performance for metrics like first-time fix rates. Running out of parts only happens when inventory management and stock control are poorly managed, which is why mastering inventory management is one of the best practices for maintenance management.
The best way to do this is to set up regular audits of your inventory so you can identify discrepancies, obsolete items and stockouts. If you also perform an ABC analysis and classify your inventory times by their value and usage, you can keep track of your items and know when to purchase more. These re-order points can then form the basis of when you decide to buy new equipment.
By following these best practices, you’ll be well on your way to taking control of your maintenance management strategy. If you’re looking to support your plan with CMMS software, please don’t hesitate to contact our team of experts.