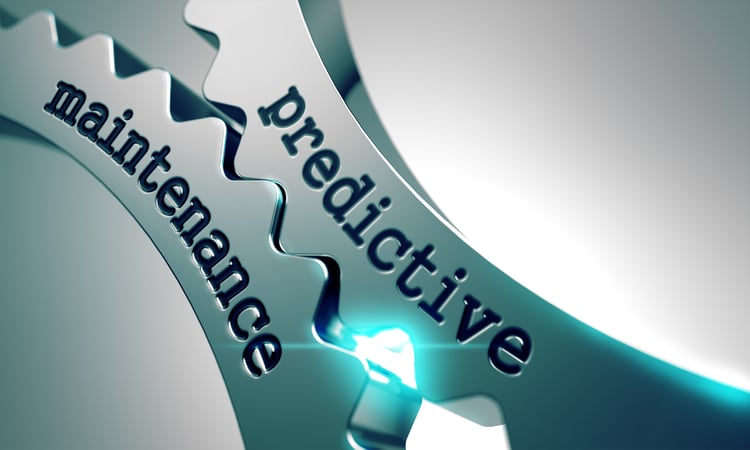
Introducing Anomaly Detection and Predictive Maintenance
Today many organisations utilise planned preventative maintenance software programmes to keep their customers’ assets in full working order. This will mean estimating and scheduling how often assets should be maintained, and executing plans of action to regularly service plant items.
Although this is effective and minimises unexpected breakdowns resulting in business downtime, the whole process of replacing and maintaining assets before they are no longer fit for use can be extremely time consuming and costly, with unnecessary maintenance becoming a major thorn in the side for small and medium sized businesses in particular
However, predictive maintenance and anomaly detection software symbolise the next step, using data science (instead of guessing) to predict equipment failures. This enables your team to identify any issues affecting the operation of your assets, no matter how small, and react accordingly.
Below we’ll break down the fundamentals and benefits of both and how Joblogic’s partnership with Shepherd to provide predictive maintenance and anomaly detection software can streamline this process.
What is Predictive Maintenance?
Predictive maintenance software, also known as condition monitoring, is a proactive approach to machine monitoring and asset management. It uses data from sensors on equipment to monitor wear and tear, temperature fluctuations etc.
Through equipment sensors, machine learning, Internet of Things (IoT) and thorough data analysis, personnel can predict if their assets are headed for a breakdown. When anomalies are detected, maintenance is scheduled before the issue becomes severe and downtime occurs. In this way, predictive maintenance helps improve asset uptime and profitability across a business’ entire fleet of equipment.
Predictive maintenance consists of the following steps:
- Choose your equipment and failure mode you want to identify
- Begin monitoring your equipment
- Once an anomaly has been identified, create a work order and assign a date
- Check to see if parts are available and allocate the job to the right technician
- Repair or replace any parts contributing to equipment failure
Using Joblogic to Streamline this Process
Joblogic (powered by Shepherd) ensures your maintenance planning runs smoothly, as equipment data like anomalies and work orders are recorded in a central virtual location.
Recorded data containing scheduled tasks and work notes are easily accessible on our app for your engineers to undertake, instantly notifying you once the job is done. Duties can include general inspections, fluid checks, equipment parts which need replacing and more – all based on the needs for your specific equipment type.
Furthemore, using our software, your technicians can survey sites and record data using a mobile app. You can distinguish equipment via a QR code, whereby engineers can directly see a product’s serial number, record model, and maintenance history. Inputting data this way helps to reduce human error associated with incorrect asset registers.
What is Anomaly Detection?
Anomaly detection is used to identify events or observations that do not conform with expected behaviour. Anomalies are identified and recorded in real-time, and in most cases, a notification is sent to the appropriate personnel.
For example, an oil refinery is known for its vast number of safety sensors. When the system detects an issue, it triggers alarms and alerts for staff to respond promptly. These systems monitor factors such as temperature, pressure and flow rate, and other safety-related issues.
This process can also be used in predictive maintenance for many purposes – from identifying faulty equipment to finding deviations with your regular workflows. Anomalies are detected using algorithms based on historical data or current performance metrics.
Lastly, anomaly detection is hugely beneficial because it helps organisations identify areas for improvement. Think of it as a data-driven secret weapon – the insights it provides helps businesses understand where to focus their efforts to achieve maximum ROI.
Use Joblogic Software to Provide a Clear Picture of Asset Data
With Joblogic, all assets and their respective data is connected to a central hub that records data in real-time. This information, stored in our anomaly detection software, can be easily accessed by multiple users to predict future failures so you can act on it.
Jobogic’s scheduling system enables your schedulers to specify how often equipment should be maintained for their respective locations. With a clear overview of all asset data, including their maintenance status and history, managers can prioritise what equipment should be maintained first and quickly deploy technicians to execute scheduled tasks.
How can Anomaly Detection and Predictive Maintenance Help Your Business?
It’s been an ordinary day on the site, where everything has seemingly run with no problems. However, a late-night call comes in informing you that a piece of equipment has failed. The result? Hours and hours of unplanned downtime, frustrated clients and lost productivity for your team.
Unfortunately, this type of scenario is all too familiar to site managers and engineers in the HVAC space. Sometimes, despite your best efforts and planning, things simply go wrong.
Using Joblogic’s predictive maintenance software, your staff can record and access data from equipment sensors and employ a proactive approach to machine monitoring and asset management. When anomalies arise, you can schedule planned maintenance to quickly rectify the problem.
Below are the main benefits of a business adopting this technology:
- Increased productivity and reduced costs due to improved equipment reliability
- Improved safety across job sites with real time alarms, alerts and notifications
- Higher cash flow through reduced equipment failure
- Improved customer satisfaction with reliable and efficient services
- Reduced carbon footprint as equipment is running consistently, using less energy and requiring fewer repairs
By using predictive maintenance, you can improve the safety of your assets while also increasing productivity. Anomaly detection software and predictive maintenance is a valuable tool for any business to have in its arsenal, and can be used in a variety of industries.
How Else Can Joblogic Help Your Operations?
As previously mentioned, Joblogic’s predictive maintenance software provides your technicians with accurate, up-to-date asset information, along with the necessary tasks needed to be done. This allows them to schedule jobs more efficiently and reduces your team’s time on site trying to figure out what’s wrong with an asset.
Additionally, once a maintenance schedule has been established, your consumers may wish to renew their maintenance contracts when they expire. Using Joblogic software, you can create reports detailing each site’s profit margins, easily determining which contracts are worthwhile. If both parties wish to renew their contracts, simply roll the dates on for the upcoming year.
Lastly, billing your maintenance work is also streamlined and simplified. Joblogic’s billing feature enables managers to easily invoice customers on their respective sites, whereby you can assign a fixed price to each job. This provides your customers with transparent pricing, allowing them to budget for service work throughout the year.
Book a free demo today to find out how Joblogic can help your business.